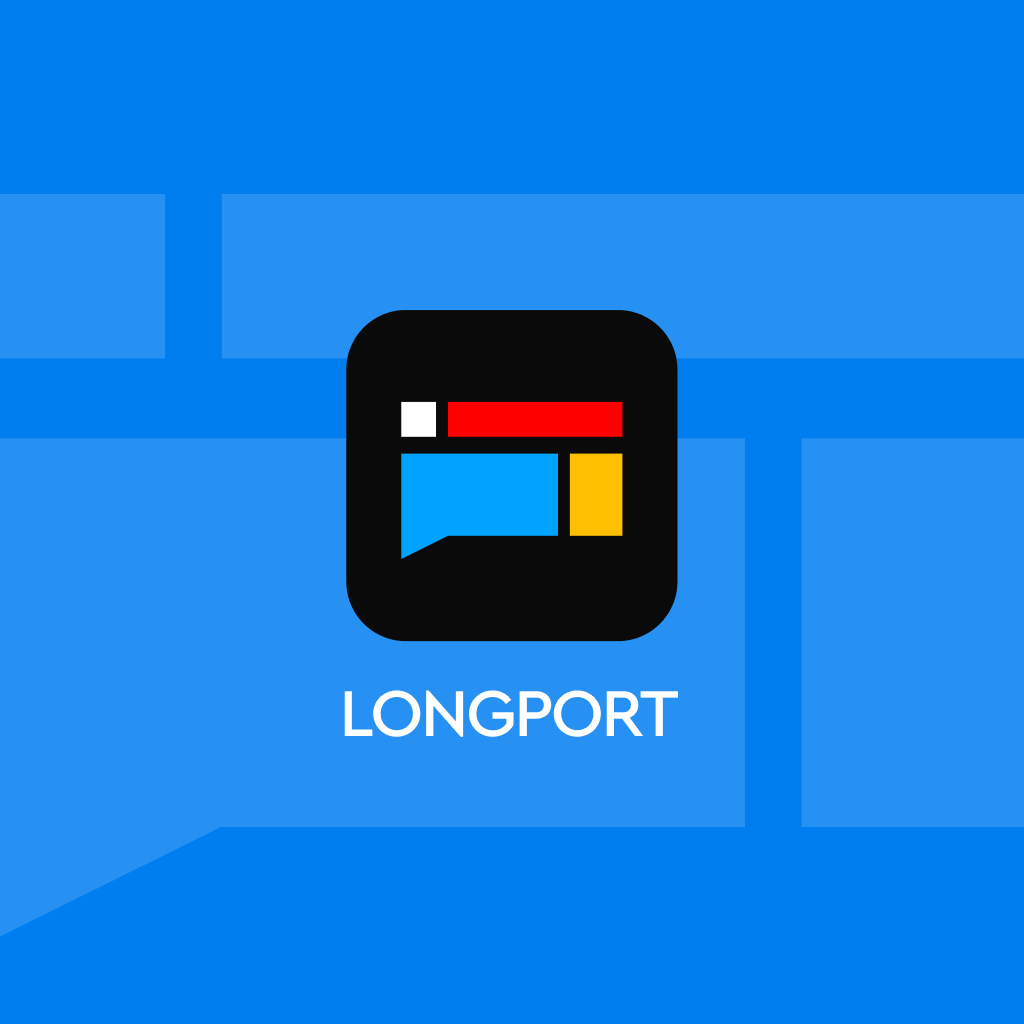
Guotai Junan Securities: Intelligent Automobile Industry Unites Upstream, Midstream, and Downstream Efforts to Expand the Potential Space for "Lightweight" Automotive Integration Casting
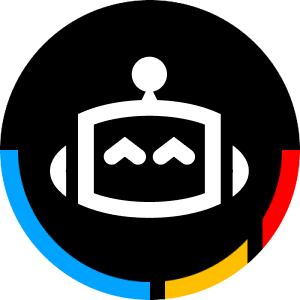
Guotai Junan Securities released a research report commenting on the integrated technology industry of smart cars. Integrated die-casting is an important technical direction, which reduces vehicle weight to meet the increasing demand for smart car endurance. Integrated batteries focus on weight reduction, with advantages in improving endurance, production capacity, and reducing manufacturing costs. The upstream, midstream, and downstream sectors are working together to expand the potential for lightweight vehicles. Integrated die-casting was first proposed by Tesla and has begun to be widely used by domestic vehicle manufacturers. Currently, collaboration in research and development along the industrial chain is ongoing, with both self-developed and procurement models by vehicle manufacturers
According to the Wise Finance APP, Guotai Junan Securities has released a research report on the integrated technology industry of smart cars. The team believes that achieving "lightweighting" through integrated technology is an important technological development direction for smart cars to improve endurance and reduce energy consumption. "Vehicle weight" is an important indicator affecting the energy efficiency of cars. Reducing vehicle weight through "lightweighting" technology can meet the urgent need for smart cars to increase endurance. In addition, integrated batteries will help with overall vehicle "lightweighting" and better economy.
The main ways to achieve lightweighting of the entire vehicle body include materials, structure, and processes. Integrated die-casting, as a comprehensive application of the three technological directions, significantly reduces vehicle weight, shortens the manufacturing process, and has become an important technological direction for achieving lightweighting in the current vehicle manufacturing sector. Integrated batteries focus on reducing weight in the three-electric system, forming clear advantages in improving endurance, mass production capabilities, and reducing manufacturing costs.
The industry upstream, midstream, and downstream are working together to expand the potential space for "lightweighting" in automobiles through integrated die-casting. Integrated die-casting was first proposed by Tesla and has been widely applied by domestic vehicle manufacturers since 2022. Based on high-pressure die-casting, integrated die-casting integrates multiple dispersed components, molds them in one casting with a large die-casting machine, and faces four main technological barriers: large die-casting machines, heat-treated materials, die-casting molds, and die-casting processes. Compared to traditional die-casting, integrated die-casting replaces the stamping and welding processes in the traditional vehicle body manufacturing process, reduces the number of parts required for vehicle body manufacturing, improves part reusability, reduces the need for manufacturing personnel and space, increases the integration of the vehicle body, resulting in a lighter and safer body, higher efficiency in mass production, and lower manufacturing costs.
Currently, cooperation and research and development are ongoing throughout the industry chain, with a parallel development of self-research and procurement models by vehicle manufacturers. Upstream heat-treated materials, die-casting machines, and mold suppliers cooperate and compete, with increasingly close connections to midstream die-casting companies and downstream vehicle manufacturers. Midstream die-casting manufacturers extend their layout upstream and expand cooperation downstream, deepening the strategic synergy between upstream and downstream. Downstream vehicle manufacturers are gradually deploying integrated die-casting technology, currently expanding research into front compartments, middle floors, and lower body assemblies. The application of integrated die-casting tests the manufacturing process development and mass production capabilities, material research capabilities, and resource capabilities. Advantages from the supply chain, equipment investment, and material research will continue to drive the deep application of integrated die-casting technology in China.
Battery factories and vehicle manufacturers are converging on integrated batteries to help with overall vehicle "lightweighting" and better economy. Power batteries have gone through the 1.0 era of standardized modules, the 2.0 era of CTP large modules, and the latest 3.0 era of CTC. Starting from improving space utilization and combining safety and economy as core requirements, the current main integrated battery technologies are CTP, CTC, and CTB.
CTP technology integrates battery cells directly into modules integrated into the battery pack, gradually entering mature application stages with product iterations. Represented by the CATL CTP product series and BYD blade batteries, both battery factories and vehicle manufacturers are working on this technology. CTB technology integrates the vehicle floor panel with the battery pack casing, aiming for battery-body integration technology CTC technology integrates the battery cell into the chassis, creating an integrated technology for the battery-chassis. CTC and CTB technologies represent different directions for the further development of CTP batteries, led by vehicle manufacturers in self-designed research and development. With technological innovation and improved production capacity, they will cultivate incremental space in the industry chain and new business opportunities.
Risk Warning: Risks include slower-than-expected overall development of the smart car market, delays in the progress and mass production of integrated technologies, and increased market competition